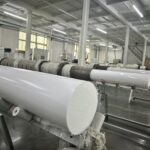
PTFE Ram Extrusion Rod
September 13, 2024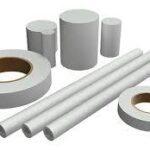
What is PTFE Product?
September 30, 2024CNC (Computer Numerical Control) machining is a precise and efficient process for manufacturing parts from PTFE (polytetrafluoroethylene) products. PTFE is well-known for its exceptional chemical resistance, low friction properties, and high-temperature tolerance, making it ideal for various industrial applications.
The CNC process for PTFE involves several key steps. First, the design phase begins with creating a detailed CAD (Computer-Aided Design) model of the desired part. This model serves as the blueprint for the CNC machine. The software translates the design into specific commands that guide the machine’s movements.
Once the design is finalized, the next step is selecting the appropriate PTFE material. PTFE can be obtained in various forms, including sheets, rods, and tubes. The chosen form is then cut to size, and ready for machining. CNC machines use rotary cutters or milling tools to precisely shape the material, allowing for intricate designs and tight tolerances.
During the machining process, controlling parameters such as speed and feed rate is crucial, as PTFE can deform if subjected to excessive heat. Utilizing coolant or air mist helps to manage temperatures and maintain the integrity of the material.
After machining, parts finish to ensure smooth surfaces and accurate dimensions. This might include polishing or additional machining operations to achieve the required specifications.
Quality control is essential throughout the CNC process. Parts are inspected using precision measuring tools to confirm they meet the specified tolerances and surface finish standards.
In conclusion, CNC machining plays a vital role in producing PTFE parts, enabling manufacturers to create high-quality components for industries ranging from aerospace to pharmaceuticals. The combination of advanced technology and material properties makes CNC machining an ideal choice for working with PTFE.