
What is the Use of FR4 Material?
November 14, 2024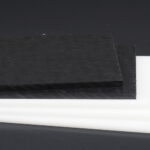
What is a POM Plastic?
November 14, 2024PEEK (Polyether Ether Ketone) plastic is a high-performance thermoplastic known for its excellent mechanical, thermal, and chemical resistance properties. While PEEK offers many benefits, it is not without its disadvantages. Understanding the disadvantages of PEEK plastic can help determine whether it is the right material for a given application.
High Cost
One of the most significant disadvantages of PEEK plastic is its high cost. PEEK is a premium material, and its production process requires specialized equipment and raw materials, which drives up the price. This makes it less economical compared to other plastics, such as polyethylene or polypropylene, and limits its use in cost-sensitive applications.
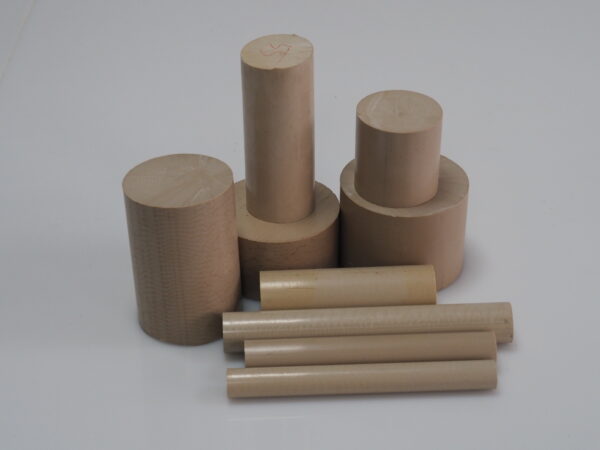
Processing Difficulty
PEEK plastic has a high melting point of around 343°C (649°F), which can make it difficult to process. The processing difficulty involves the need for specialized machinery and high temperatures, which increases energy consumption and manufacturing time. This can lead to longer lead times and more expensive production processes, particularly for small-scale or complex parts.
Brittle Under Certain Conditions
While PEEK is known for its toughness, it can be brittle under certain conditions, especially when exposed to extreme temperatures or mechanical stresses. At low temperatures or after prolonged exposure to high stresses, PEEK may become more prone to cracking or breaking, which limits its use in certain structural applications.
Limited Availability
PEEK plastic is not as widely available as more common materials like polyethylene or PVC. This can create challenges in sourcing, especially for large-scale or international projects. Furthermore, its specialized nature may require custom formulations, which could add to lead times and costs.
Conclusion
In conclusion, the disadvantages of PEEK plastic, including its high cost, processing complexity, brittleness under certain conditions, and limited availability, can make it less suitable for some applications. However, for high-performance environments requiring excellent thermal, mechanical, and chemical properties, these drawbacks may be outweighed by its many advantages.